New Building Technologies and Housing Solutions
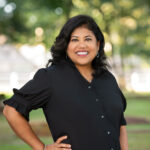
By Nushin Huq
9 min read
Streamlining Construction and Design Projects
The latest technological innovations, such as robotics, artificial intelligence (AI) and 3D printing can alleviate construction industry challenges and save time and costs from projects.
Labor shortage remains one of the biggest challenges in the construction industry, leading to increased costs and the length of time it takes to complete a project.
Today’s Newest Innovations
The newest technology is moving a lot of onsite framing construction toward a factory setting, says Jess Lohse, executive director of the Structural Building Components Association and the National Framers Council.
The groups’ members produce structural framing elements, called components. These include wall panels, floor and roof trusses.
Factory-made components fall under the same building code as onsite framing construction. While the process can still be manual, factory construction replicates onsite construction in a manner that’s ergonomically better and in an environmentally controlled facility, and recent innovations include more automated machinery and robotics. These robots can perform tasks, such as picking the raw material, cutting it to length and the proper shape and inserting it into the jigging equipment.
One of the most recent innovations is a floor cassette, says Lohse. Floor sheeting is applied on top of individual floor joists or trusses in the factory. That floor cassette can be delivered to a job site and lifted in place with a crane to where it will sit permanently on the structure.
“It saves a lot of time,” Lohse says. “Skilled labor is becoming more and more difficult to find, so being able to utilize these methods can really speed up the production time on the job site.
Robotics and the Real-Time Evaluator
The latest in robotics allows manufacturing facilities to be customized for the capacities of the buildings, levels of automation and cutting to optimize lumber and reduce waste, says Lohse.
Looking ahead, Lohse sees that robotics will not only become more advanced and have a higher industry adoption rate but will also use AI to aid in the design of the most efficient framing solution.
For example, using AI, building designers can iteratively try five different options on how structural elements are laid out and find the most efficient options to maximize structural performance, Lohse says.
AI is already being used in real estate acquisition. California-based ProforMap uses AI for commercial real estate acquisition, targeted especially for affordable housing builders. The platform uses data analytics and mapping technology to help developers identify affordable housing opportunities that are in line with local, state and federal housing policy. The platform also has 3D modeling capabilities of potential projects on properties, carries out proforma analysis and helps users find a broker. ProforMap currently only has properties in California, but the company aims to have them available for all of the U.S. by the end of the year.
At Oak Ridge National Laboratory (ORNL) in Tennessee, researchers are working on developing a real-time evaluator. Once completed, the tool will provide accurate measurements and positioning directions for insulated prefab panels that are installed on the exterior of existing buildings to improve their thermal, airtightness and water-tightness performance.
The goal of the system is to identify the location of the panels while they are being installed using an autonomous robotic tracker and compare it to the information that is in a digital twin, says Diana Hun, a researcher at ORNL. Advanced algorithms generate real-time positioning feedback for installers to minimize errors and expedite installation.
“With that, we are providing real-time feedback to the installers of the panels, Hun says. “So that they know how to improve the placement and meet tolerances in a shorter amount of time.”
The real-time evaluator will be applicable to any type of prefabricated construction, Hun says.
In a sister project, ORNL researchers are working to increase the efficiency of building envelope retrofits using modular overclad panels that are installed on a building’s exterior.
“In our case, the innovation is that we’re using fiber-reinforced composites as the facers that will clad foam insulation,” Hun says. “This allows us to attain panels that are lighter than others in the market. They’re also thinner because these facers also have structural capabilities. We can tailor the amount of reinforcement based on the structural capacity that we need.”
The panels and the real-time evaluator will be used at a Knoxville, TN project retrofitting affordable housing duplexes. The technology package that includes the fiber-reinforced overclad panels, variable refrigerant flow (VRF) heat pumps, heat recovery units and heat pump hot waters will reduce the buildings’ thermal loads by about 75 percent.
3D Printed Homes
ORNL is also collaborating with the Advanced Structures and Composites Center (ASCC) of the University of Maine on the 3D printing of homes as part of the Sustainable Materials and Manufacturing Alliance for Renewable Technologies (SM2ART). Researchers collaborated with UMaine’s ASCC to construct a 600-square-foot modular home on the center’s campus using the world’s largest 3D polymer printer, manufactured by Ingersoll Machine Tools, says Halil Tekinalp, a researcher at ORNL.
Made with fully bio-based polymer composites, researchers have added sensors to the house to simulate someone living in it and are currently collecting data over the next two years.
In the future, this technology could also be used in multifamily construction with additional floors, Tekinalp says.
Ready-to-Install Kits for Building Interiors
In June, the Structural Building Components Association, ORNL and ProforMap participated in the Innovative Housing Showcase organized by the National Association of Home Builders and the U.S. Department of Housing and Urban Development. The showcase featured new building technologies and housing solutions. Also among the participants was San Francisco-based Kit Switch, which delivers kits from its library of ready-to-install interiors for tenant improvement, retrofit and conversion projects.
Founded in 2021, by two-woman co-founders, Kit Switch offers a solution to improve turnaround, predictability and sustainability on the design, construction and rehabilitation of our buildings’ interior spaces, says Candice Delamarre, co-founder & chief operating officer. With its first product, the Kit-Kitchen line, cooking amenities can be installed or reconfigured on-site in less than one day.
“It’s well suited for the multifamily and affordable housing market because we have created a library of standardized products, which can be manufactured at scale for cost and time efficiency, all while ensuring quality and sustainability,” Delamarre says.
“While we created Kit Switch as a kit to switch the use of existing buildings, our products and processes are effectively also applicable to new builds.”
The Kit Kitchen is made of three blocks – a cleaning module, a cooking module and a storage module. The design and packaging of the kits make it easy to move through the doorways and hallways of most buildings. Within a kit, the modules function together thanks to a panelized system, which simplifies installation and trade coordination.
“This means on-site contractors do not need to spend a lot of time on precise finish work. Instead, they can follow our guidelines to quickly prepare the wall and systems before the delivery of our products. All the finish work is handled by Kit Switch. In parallel with on-site preparation work, the production of finished interior products is completed in the facility where quality control is ongoing, scheduling is easier than site coordination and material utilization is optimized for waste reduction,” Delamarre explains.
“Pain points, like trade coordination, are things my co-founder and I have noticed on job sites. For instance, kitchen drains needed to be moved because of a misalignment issue with the carpentry or electrical work,” Delamarre says.
“It is hard to coordinate all the different workers involved in a project. Building interiors can involve anywhere from three to ten different trade specialties,” she says. “Using our all-in-one kits makes it easier for project managers to handle scheduling and coordination. Design specifications have been established upfront with the developer and architect during our design phase when they pick their kit. And since each module was already designed to comply with building codes, they can be delivered, laid out, following our design, and installed – all in a simple and predictable manner.”
Novin Development Corp. recently used Kit Switch on two projects in the San Francisco area. The first project was a 33-unit preservation of affordable housing for which Kit Switch provided modules for the remodel of one apartment unit.
“It was a great experience,” says Iman Novin, president of Novin Development Corp., as well as ProforMap. “We found a lot of savings on plumbing, electrical and drywall removal.”
In traditional Kitchen rehab projects, even with inexpensive cabinets the process is more expensive because of the added cost to reframe and redo drywall, plumbing and labor, Novin says.
“We found that Kit Switch ended up with a much cleaner product and our labor costs were a lot lower,” Novin says.
Novin estimates that using Kit Switch was 20 to 30 percent less expensive and 30 to 40 percent faster than a traditional kitchen conversion project.
The current focus at Kit Switch is on scaling its first product line to several project types including multifamily rehabs, motel conversions, affordable housing and student housing. They are actively looking for projects that are five to ten units for Q3 and Q4 2023, and 50+ units for 2024. Past and upcoming pilots are tracked with the support of the National Renewable Energy Lab, and a long list of incubators, including the Wells Fargo Innovation Incubator, the Los Angeles Cleantech Incubator, USGBC-LA’s Net Zero Accelerator, the Larta Institute’s Venture Fellows program, as well as the Housing Lab.
Future pilots will see the addition of new kits to its existing library. Kit Switch is looking to connect with developers, architects, contractors and other stakeholders with relevant projects and an interest in its product.